SORALUCE Duplex Machines
DUPLEX milling machines are two machines located one opposite the other, which can work separately or as a single milling machine, when workpiece can be machined with 2 simultaneous spindles.
Main advantages of duplex solution:
- Production increase of up to 50% in relation to conventional solutions, i.e. individual milling machines
- Improvements in part precision, by managing to do the machining of the part in one single setup, in most of the cases
- One sole operator can control the DUPLEX milling machines
- Reduced space and investment requirement comparing with two single machines
- Fast investment amortisation due to the high productivity
- Duplex solution admits different configurations: single working area, pendulum working areas or pallet changing system
DUPLEX PACK by Soraluce:
Specific cycles and options by Soraluce:
- Double control panel to operate both machines from a single position and only by one operator
- Synchronization of the CNC programs to increase productivity
- Fixed points search cycles
- Transmission cycle of zero points between the machines
- M functions for program synchronism
- Anti collision system
Customisation
Select your head:
Technical data
It enables for:
- Automatic indexing of vertical and diagonal articulations.
- Automatic tool changing.
- Automatic head changing.
- Internal / external cooling system.
- Suitable for any type of taper and pull-studs.
- Different clamping forces for different tools.
- Suitable for setting different accessories.
- 32 / 43 / 46 / 55 kW
- 2.5° x 2.5° / 1° x 2.5° / 0.001° x 0.001°
- 4000 / 5000 / 6000 / 7000 min-1
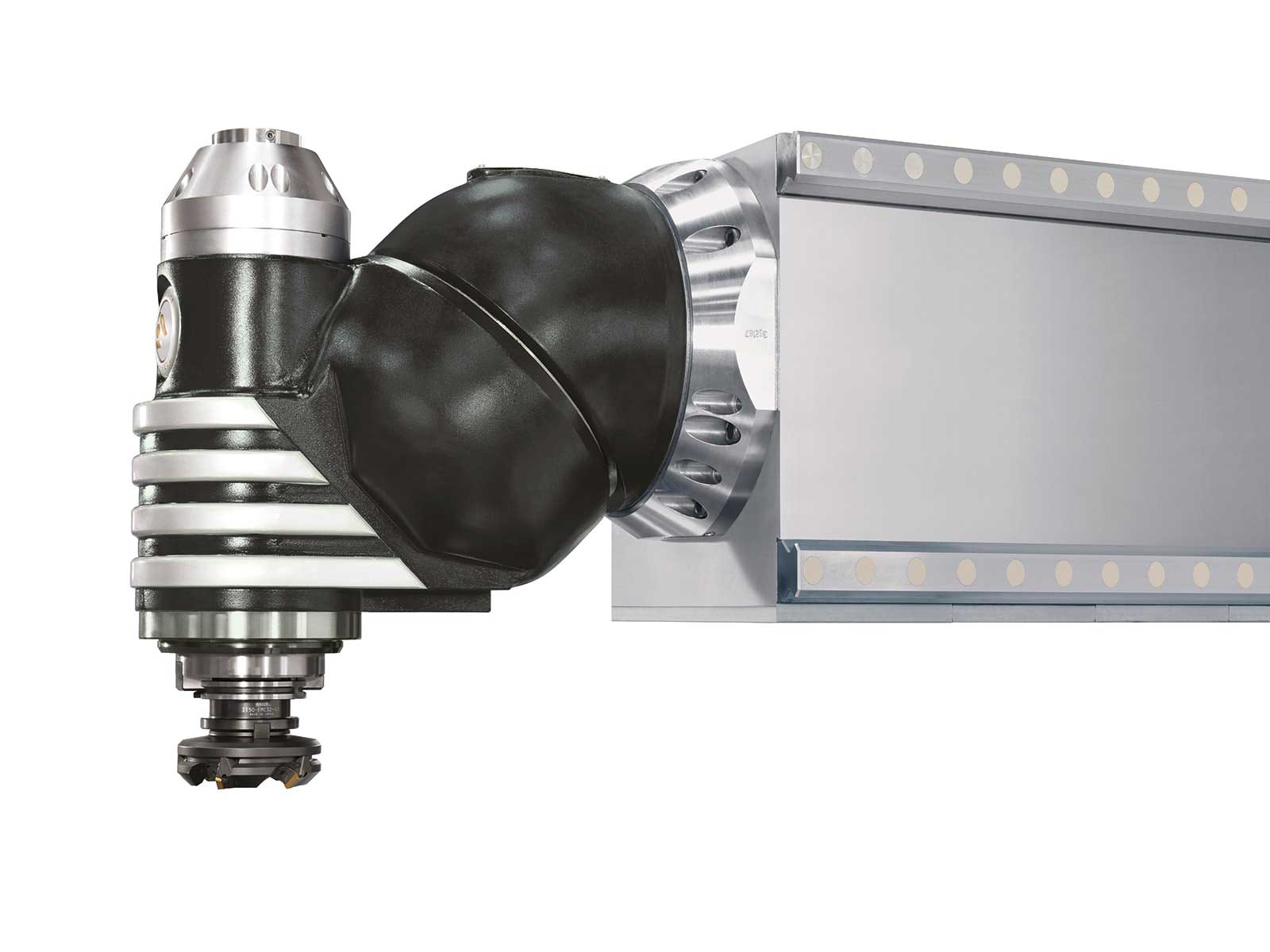
Technical data
Its compact design is specially conceived for machines with an in-line motor. It allows the simultaneous positioning of both head articulations, reducing non-production time.
Inverse machining capability:
- Up to -45º
- No additional setups
- Improved cycle time
- Better finishing quality
- Minimum manipulation
- Full advantage of machine travel
- No need for additional work piece support fixtures
- Close to table head spindle accessibility for both front and lateral milling
- 37 / 43 kW
- 1º x 1º
- 4000 min-1
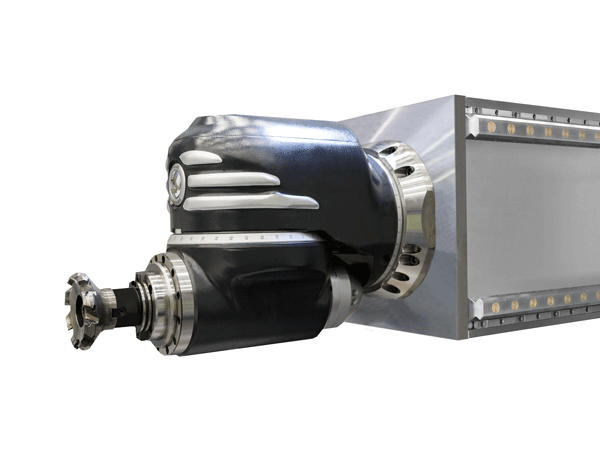
Technical data
It enables for:
- Automatic tool changing.
- Automatic head changing.
- Internal / external cooling system (no external tubes exposed to chips).
- Suitable for any type of taper and pull-studs.
- Different clamping forces for different tools.
- Suitable for setting different accessories.
- Flexibility
- Interchangeability
- Options
- C Axis
- Maintainability
- 43 / 46 / 49 / 81 / 106 kW
- 2000 / 3000 / 4000 / 5000 min-1
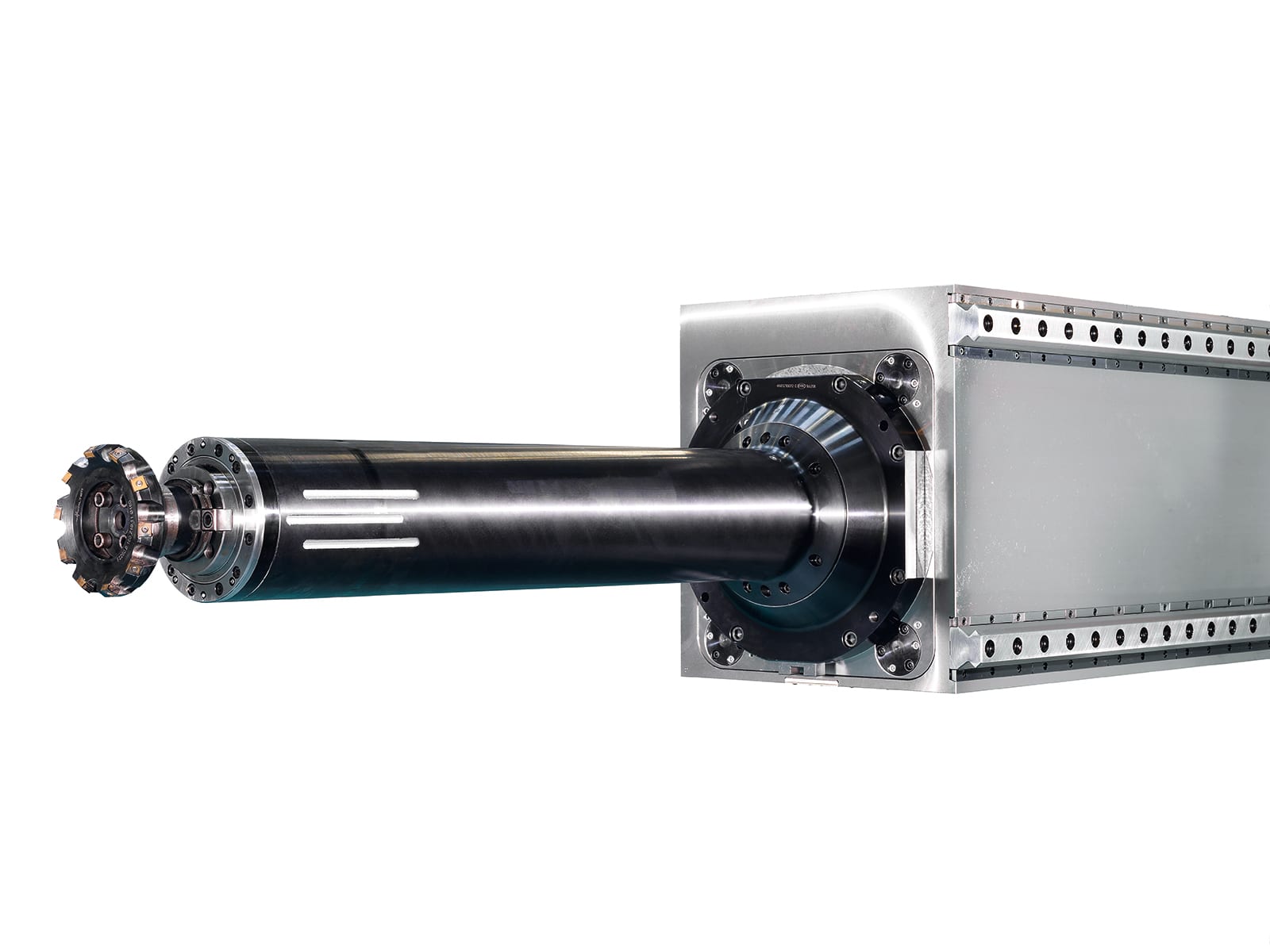
Technical data
- Automatic indexing head with turning capabilities
- Up to 4000 rpm with standard steel bearings, or 5000 rpm with hybrid bearings
- Air-oil lubricated gears
- The head includes a clutch in the spindle area for positioning and clamping the spindle at any angle for turning operations. The clutch hydraulically clamps and unclamps the rotation of the spindle for turning operations
- Possibility of working with bigger diameter workpieces, performing turning operations in a diagonal direction (interpolation X/Z axes)
- The head can be positioned to avoid interferences with the workpiece
- The use of this head is highly recommended on multitasking machines (milling and turning)
- 37 kW
- 2.5° x 2.5° / 0.001° x 0.001°
- 4000 / 5000 min-1
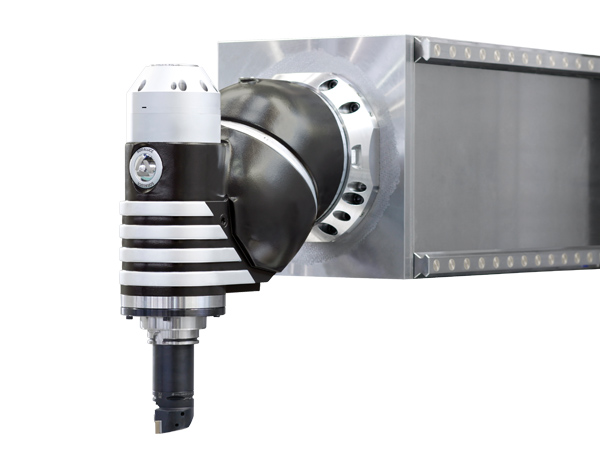